General Type
Wood Screw

Wood screws are probably your most general type of screws. They are characterized by having a sharp tip to help start the screw without the need to pre-drill. They will also, typically, have coarser threads (fewer threads per inch).
Drywall Screw

Image by lowes.com
Drywall screws have a bugle head style (see below) which makes them ideal for attaching drywall to WOOD studs (not for use with metal studs). Drywall screws can be used as a wood screw but not vice versa. They are very similar to wood screws so be sure that you double check before buying.
Metal Screw

Image by lowes.com
Ideal for attaching metal to metal and wood. Metal screws are similar to wood screws with a couple key differences. Metal screws tend to have more threads per inch and also usually have a flat head type i.e. pan, round etc. (see below for head types)
Machine Screw

Image by lowes.com
Machine screws are used in, you guessed it, machines. These screws generally won’t have a point to them because they are inserted into a pre-existing hole. These screws will often come with nuts to thread onto the other end once the screw has been threaded through the machine.
Concrete Screw

Image by lowes.com
You might hear someone say Tapcon screws when referring to a concrete screws but Tapcon is simply the brand name (think Jacuzzi/hot tub). These are usually seen with twin start threads of the high-low variety (one thread that’s “high” and one that’s “low”). You will also find that most concrete screws will be blue or sometimes orange.
Anchor Screw

Image by lowes.com
This is a pretty broad category, but I wanted to include it here to give you a little exposure to it if you’ve never seen one before. The picture to the left is of a drywall anchor (one of many different types). These are inserted into a pre-drilled hole in the wall, then tightened down. When tightened, they will pull the red piece of plastic towards the head of the screw which then bends the thin metal surrounding the screw and compresses it to the back of the drywall.
Head Type
Countersunk

Image by lowes.com
If you are needing to have a screw sit flush with the material, like you would when building a deck, you need a countersunk screw. Another common way to have a screw fit flush with your material is using a countersink drill bit. This screw takes that step out of the equation.
Bugle

Image by lowes.com
Technically another style of a countersunk screw. The bugle shaped screw is most commonly used for drywall. The soft curve of the bugle screw head is easier on the paper of the drywall and will minimize any damage to the drywall.
Round

Image by lowes.com
Rather than sitting flush with the material, round heads are going to sit above the material when screwed in rather than flat with the material. For this reason, these heads are not common when working with wood. They are usually found on machine and metal screws where countersinking isn’t always an option.
Pan

Image by lowes.com
Pan heads are nearly identical to round heads in both looks and function. The pan head is going to have a flat surface on the top of the head and rounded sides (just like a kitchen pan).
<
Drive Type
Flat Head

Image by lowes.com
Characterized by a single slot across the head of the nail, the flat head has no primary feature other than being practical (in production that is). The flat head was one of the earliest drive types. Since then, engineers have found far better ways to fasten screws.
Phillips

Image by lowes.com
Invented in the 30’s by John P. Thompson (later sold to the Phillips Screw Company). The Phillips head was designed to increase ease of alignment between driver and screw, and reduce the possibility of stripping the material you are fastening. It does this by intentionally pushing the driver out of the head if the screw is under too much torque. Ironically, this very reason is why most people dislike this drive style.
Pozidrive

Pozidrive is very similar to the phillips but has two primary differences. First, and most noticeable, are the small cuts made between the primary slots. The second difference is that the sides of the slot are parralel to each other as opposed to the phillips where the slots start wide and become more narrow towards the bottom. It is this V shaped design that helps the phillips driver cam out of the phillips screw. Since the pozidrive has parallel sides it does not cam out (as much) which increases the amount of torque you can apply to the screw.
Triangle

Generally called a “triangle” drive, the TP3 triangular recess drive is designed as a tamper resistant screw. You will rarely come across these screws but if you do it will likely be in cheap chinese toys (for some reason). Even more difficult is finding a driver for these types of screws. They don’t sell them at your local hardware store. Or Lowes…Or Home Depot. Seriously guys they’re hard to come by, but you can get a set from amazon.
Robertson

The robertson screw, named for it’s canadian inventor Peter Lymburner Robertson, was invented after he injured his hand with a flat head style driver. This drive style became highly regarded in the industry. It is self centering, it makes a tighter fit which reduces cam out and increases possible torque, and it reduces possible damage to product during manufacturing. These screws can still be found in products today but are being replaced with even better screws.
Torx

Torx aka star drives (think Jacuzzi/hot tub again) are seen in numerous places from vehicles to hard drives. This style of driver was specifically designed to prevent cam out. Another common feature with these screws is the security version which has a tiny pin in the center of the slot, preventing a regular driver from fitting.
One Way

Image by homedepot.com
One way screws are the original security screw. Invented in the early 1900’s, this style of screw was the leading security method for many decades. While they can still be found today, they have been largely replaced by more secure and more practical screws like the Torx security screw mentioned above.
Material
Steel

The most common material for screws and is used for just about everything that you’re going to come across. While the steel screw is by far the most common, there are a few times when you need a different type of screw.
Silicon Bronze

Image by boltdepot.com
Commonly seen on boats and other marine equipment due to their superior corrosion resistance but they are becoming more and more rare as they are being replaced with stainless steel. Other reasons for use are primarily for asthetic purposes.
Brass

Image by boltdepot.com
Brass is commonly used for it’s aesthetics, due to brass having a shiny gold or tan appearance, and for it’s soft properties to avoid damage to other delicate metals. It is also very resistant to corrosion and will therefore be seen where water is typically present (so long as a strong connection is not required).
Aluminum
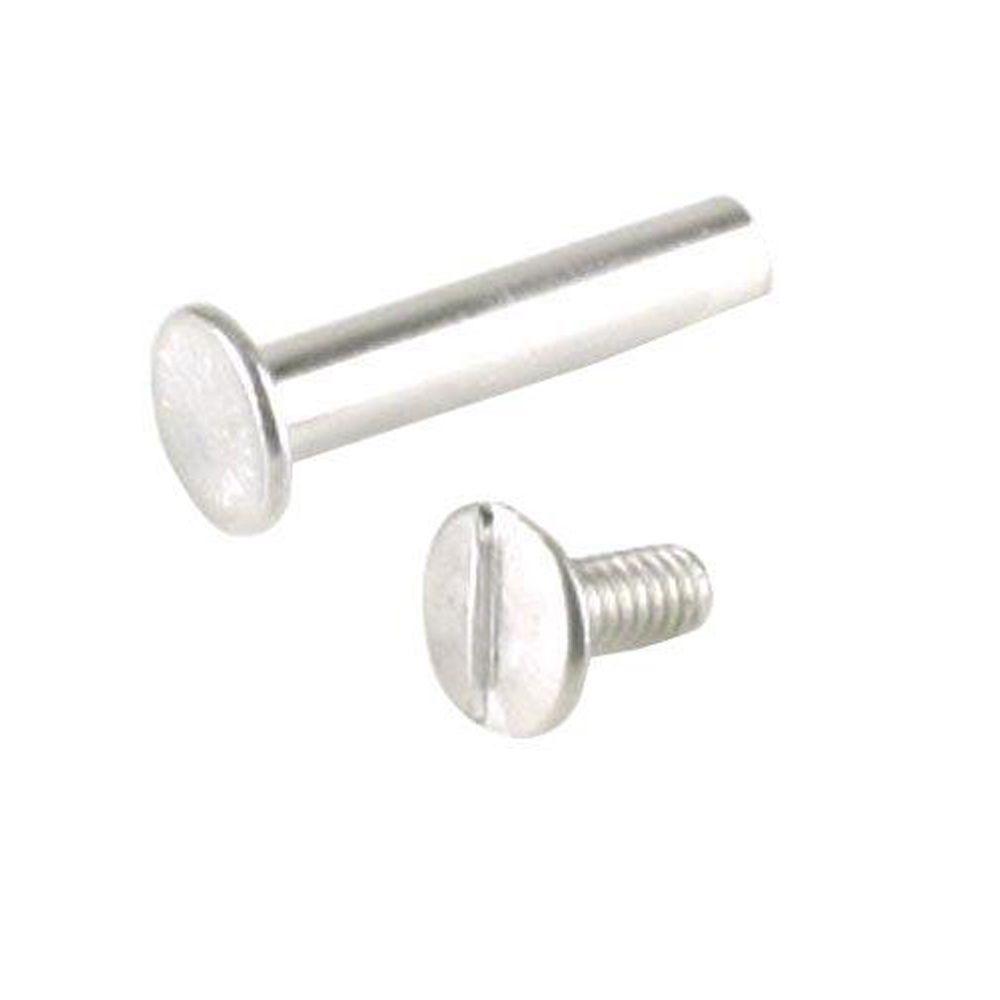
Light weight, aesthetically pleasing, corrosion resistant and cheap. Aluminum offers many advantages over other materials and is seen virtually everywhere from cars (to keep weight down) to refrigerators (for corrosion resistance). However, along with brass, they are too weak to be used in jobs requiring support for a heavy load.
Titanium

One of titanium’s most useful properties is its high tensile strength to density ratio. It also happens to be the most common type of screw to be found in a person! Titanium screws are used in many different surgical procedures including knee replacements and bone fractures.
Plastic
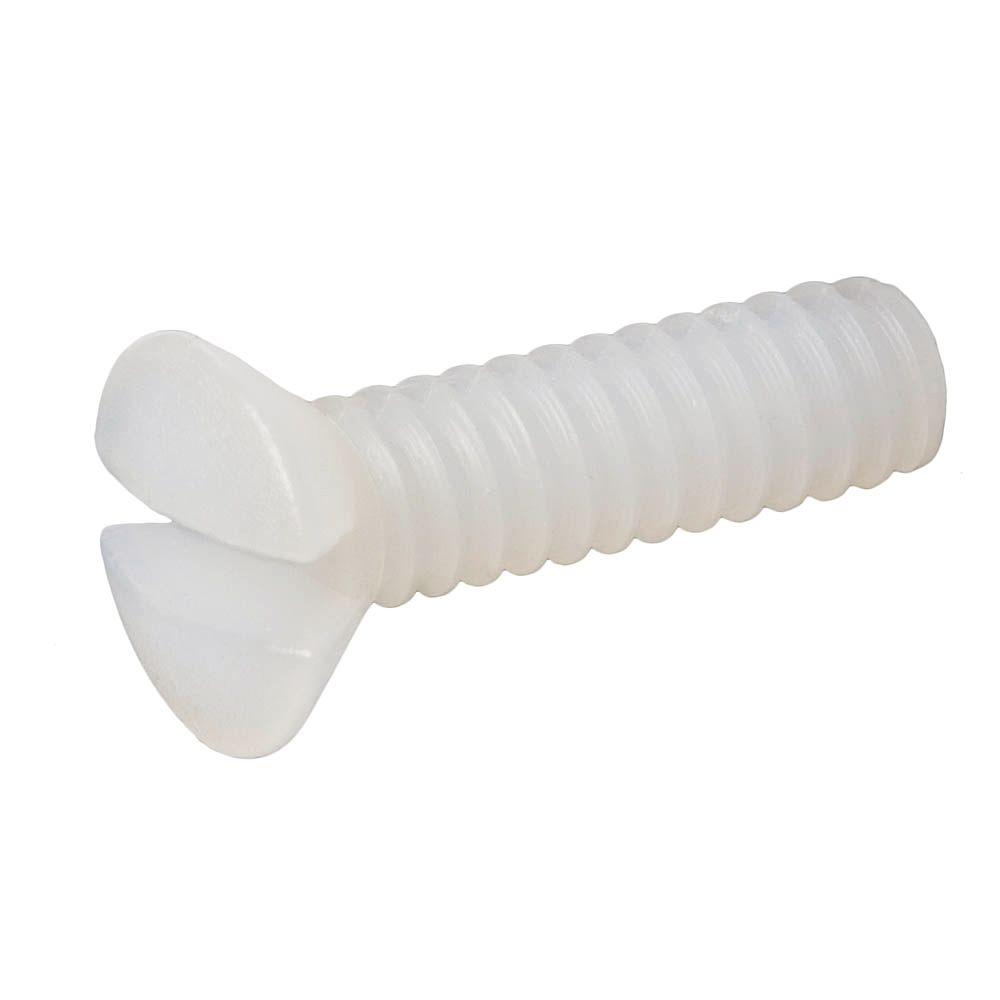
Image by homedepot.com
Plastic screws aren’t very common but do come in handy when you’re fastening something to a very soft or fragile material. When fastening a toilet seat to a toilet you will almost always find that you will use a plastic screw so that you do not damage the porcelain. They can also be found when fastening plastic to plastic. One of the coolest things about plastic screws is that they can be 3D printed right at home!
Wood
This is probably going to be the rarest screw material you are likely to see, especially as a traditional screw with an actual head. Usually they are going to be seen in wood clamps or similar devices.
Finish
Plain (No Coating)
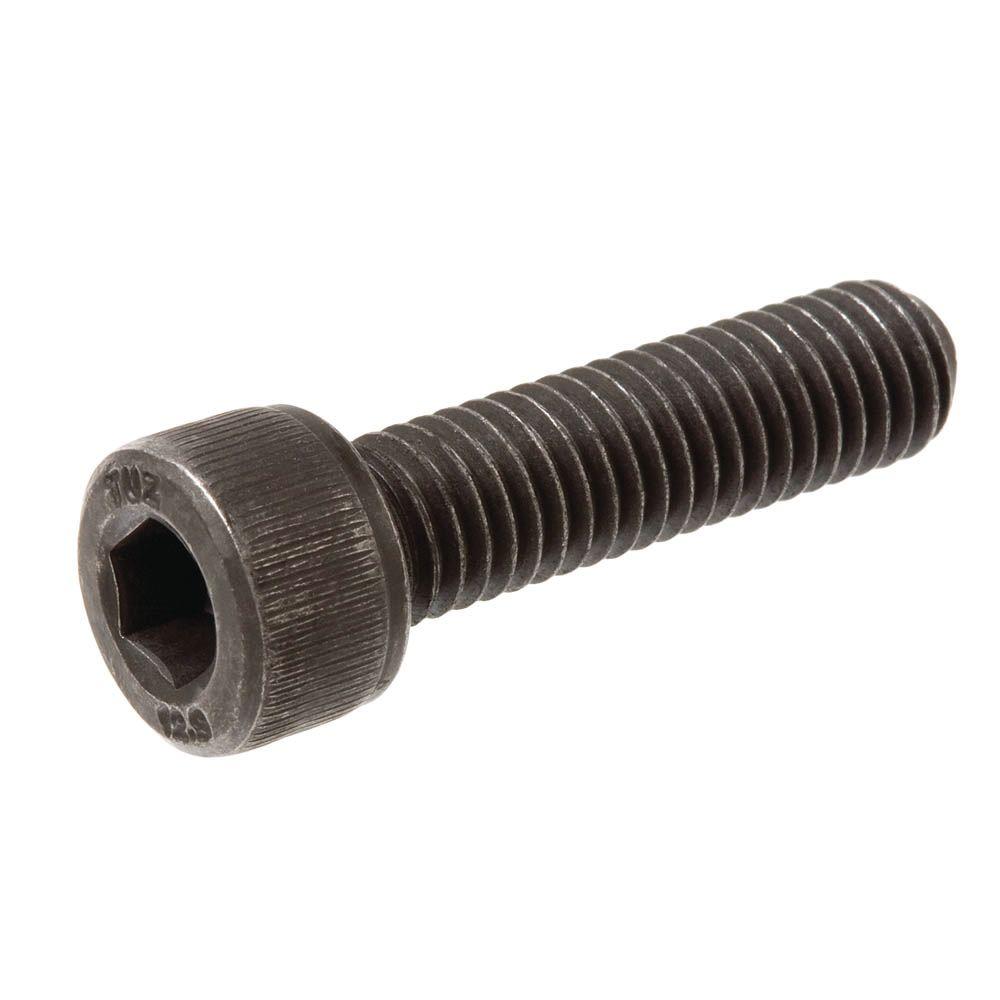
Image by homedepot.com
When it comes to steel screws, it’s rather difficult to find them without a coating. This is because steel is pretty susceptible to corrosion without a coating. However, when it comes to all other materials, you will generally find that they all come plain without a coating. This is because when a special material is used, like brass for example, it is being used specifically for the properties brass has to offer (not because of its strength like steel).
Hot Dip Galvanized

Image by boltdepot.com
A very popular coating for outdoor products. Hot dip galvanized screws are cost effective and do a very good job preventing corrosion. Made in a process where zinc is heated to above 800 degrees and steel is then bathed in the zinc. While this process uses zinc, it is not the same as a zinc coating.
Zinc
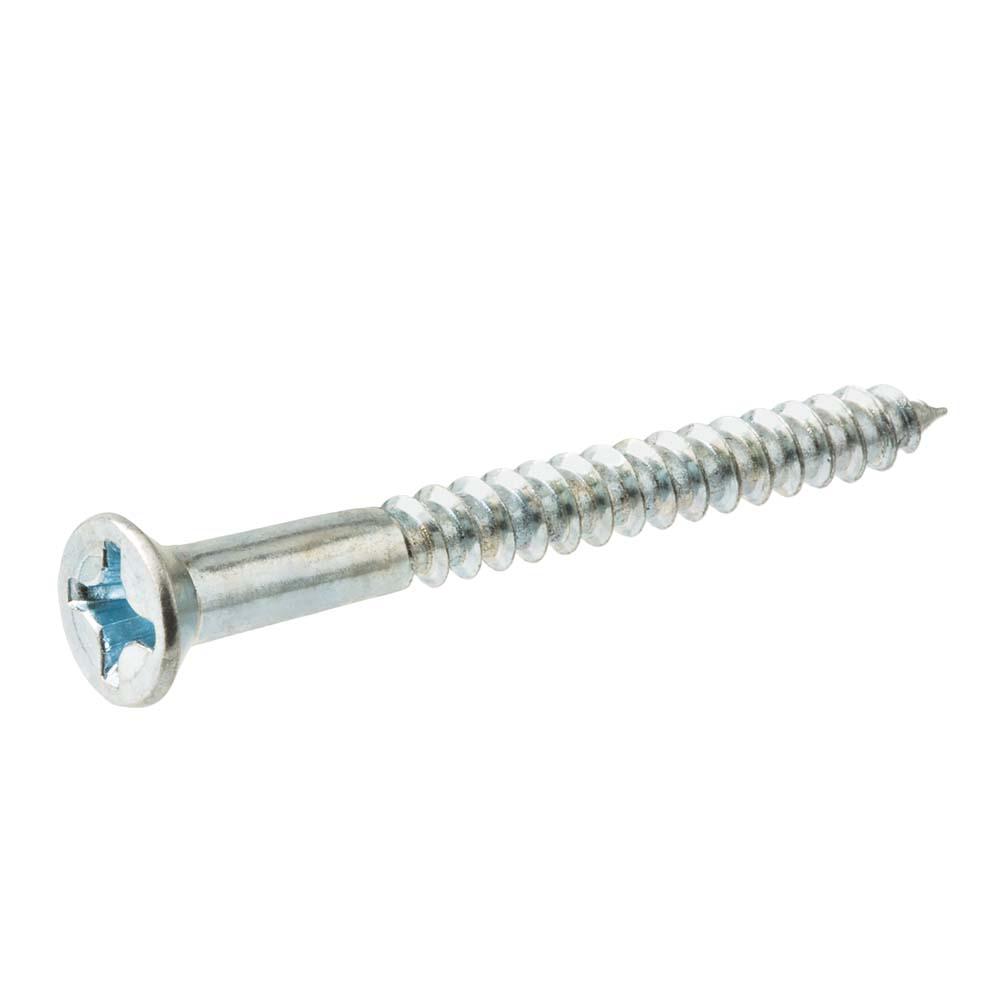
Image by homedepot.com
A zinc coating of course uses zinc to coat the screw but goes about it in a different way than the hot dip galvanizing process. Zinc plating is done through a process called electroplating. This results in a thinner coating of zinc on the material. Because of this is not as durable as a galvanized screw but it does have the added advantage of having a more aesthetically pleasing appearance.
Chrome

Image by boltdepot.com
Think car bumper but way better. The chrome that’s used on screws is a lot harder and more durable than what is used on a car bumper. This coating solves many problems. It’s very corrosion resistant, durable, and cost effective and it doesn’t hurt that it’s one of the most aesthetically pleasing options out there.
Copper
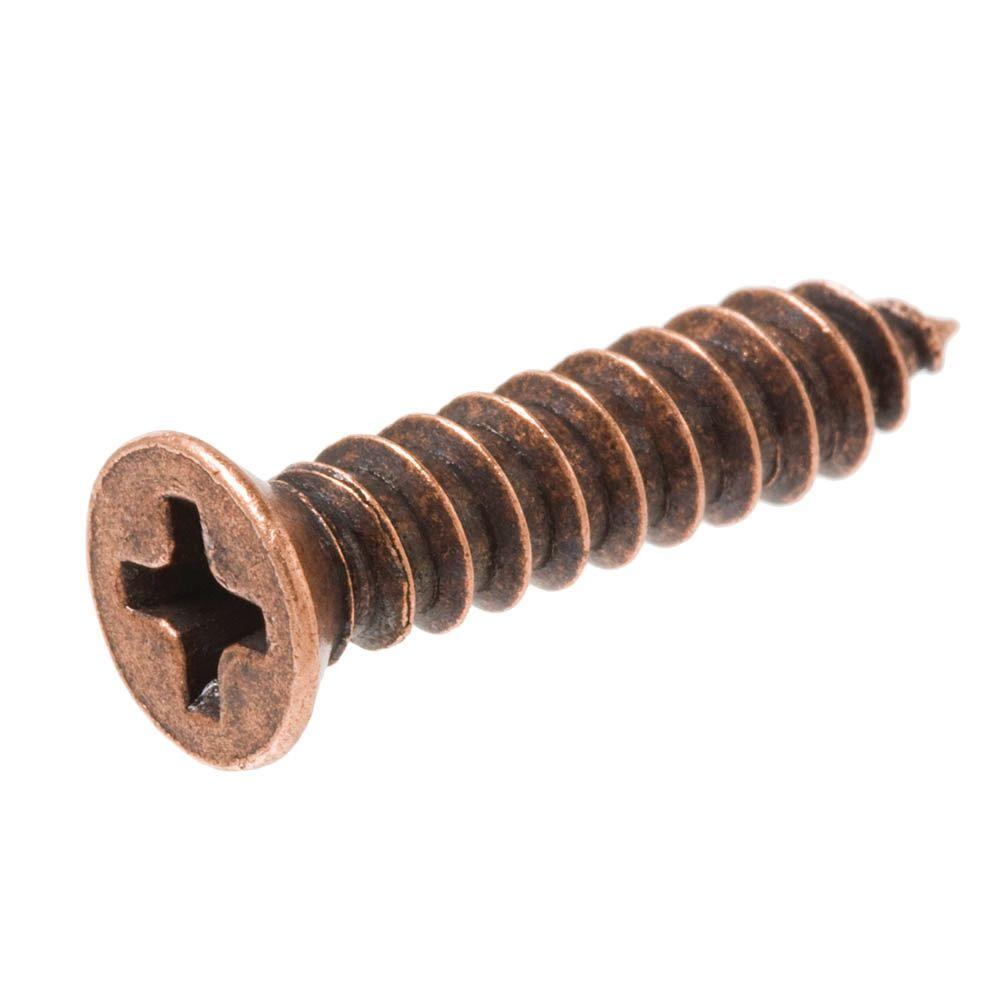
Image by homedepot.com
Like all other coatings, it is a good option for corrosion resistance. However, what copper has to offer that the other coatings don’t is that copper happens to be a very electrically conductive material only being outperformed by silver.
Nickel
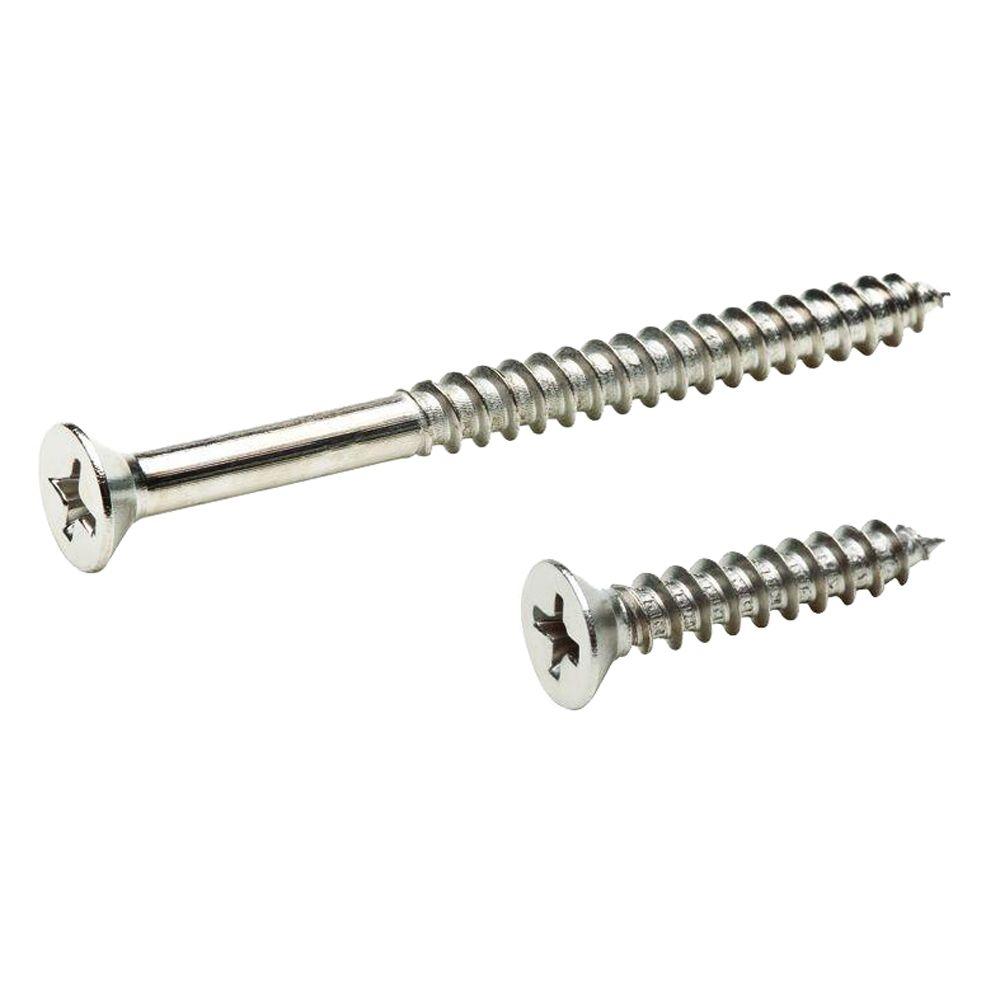
Image by homedepot.com
A primary use for nickel plating is for its looks and will commonly be seen applied over copper and under cadmium for decorative purposes. It also has the unique property of creating a magnetic effect when applied.
**This is NOT comprehensive! There are many, many more types of screws**
Sources
pbswisstools.com
boltdepot.com
wikipedia.org/wiki/screws
collectionscanada.gc.ca
wikipedia.org/wiki/Torx
brycefastener.com
aftfasteners.com